And finally… no dry stone too high
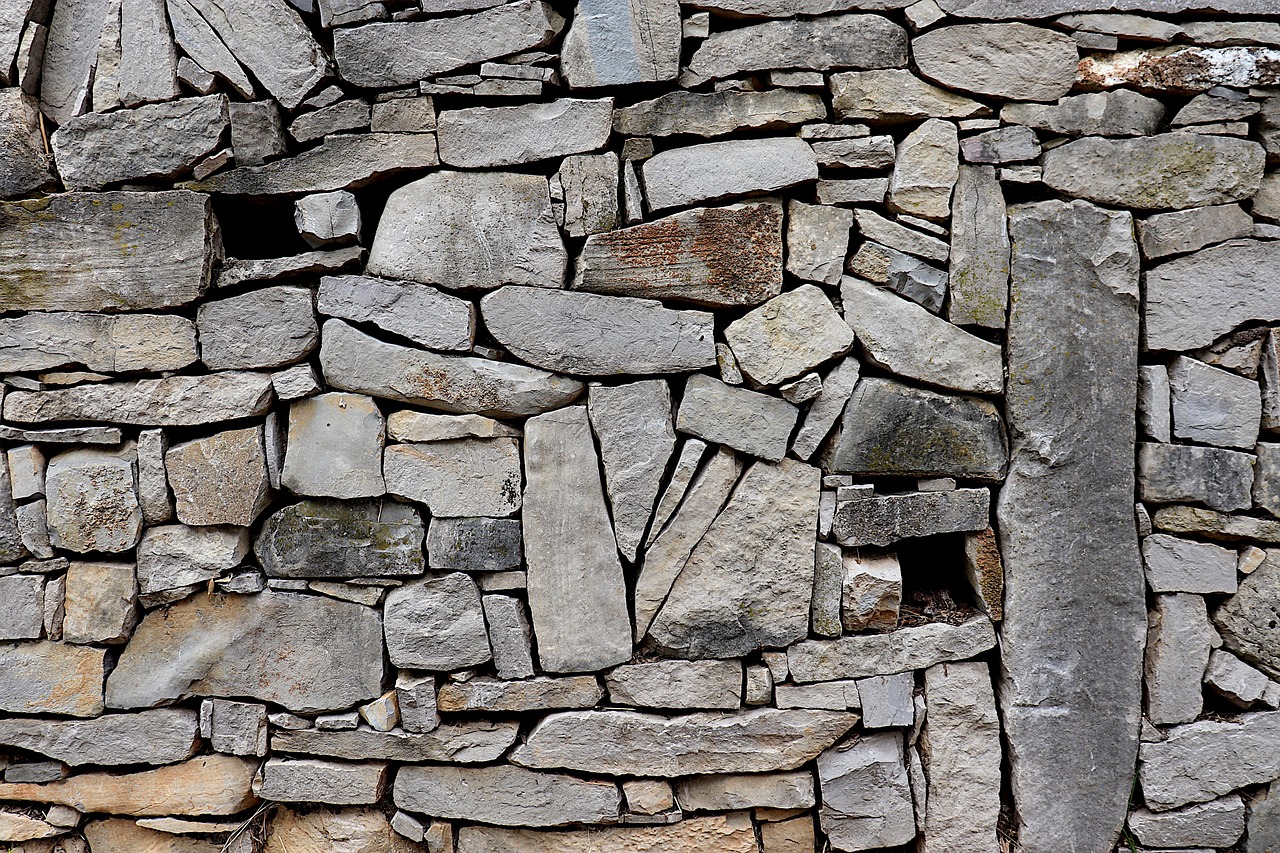
An autonomous excavator has been taught to construct dry stone walls itself using boulders weighing several tonnes and demolition debris.
Researchers at ETH Zurich deployed an autonomous excavator, called HEAP, to build a six-metre-high and 65-metre-long dry-stone wall. The wall is embedded in a digitally planned and autonomously excavated landscape and park.
The team of researchers included: Gramazio Kohler Research, the Robotics Systems Lab, Vision for Robotics Lab, and the Chair of Landscape Architecture. They developed this innovative design application as part of the National Centre of Competence in Research for Digital Fabrication (NCCR dfab).
Using sensors, the excavator can autonomously draw a 3D map of the construction site and localise existing building blocks and stones for the wall’s construction. Specifically designed tools and machine vision approaches enable the excavator to scan and grab large stones in its immediate environment.
It can also register their approximate weight as well as their centre of gravity. An algorithm determines the best position for each stone, and the excavator then conducts the task itself by placing the stones in the desired location. The autonomous machine can place 20 to 30 stones in a single consignment – about as many as one delivery could supply.
“Automated building processes that enable efficient in situ resource utilization can facilitate construction in remote locations while simultaneously offering a carbon-reducing alternative to commonplace building practices,” the researchers explain in the abstract to their paper. “Toward these ends, we present a robotic construction pipeline that is capable of planning and building free-form stone walls and landscapes from highly heterogeneous local materials using a robotic excavator equipped with a shovel and gripper.”
“Our system learns from real and simulated data to facilitate the online detection and segmentation of stone instances in spatial maps, enabling robotic grasping and textured 3D scanning of individual stones and rubble elements,” the researchers explain. “Given a limited inventory of these digitized stones, our geometric planning algorithm uses a combination of constrained registration and signed-distance-field classification to determine how these should be positioned toward the formation of stable and explicitly shaped structures.”