Brick made from waste achieves industry certification
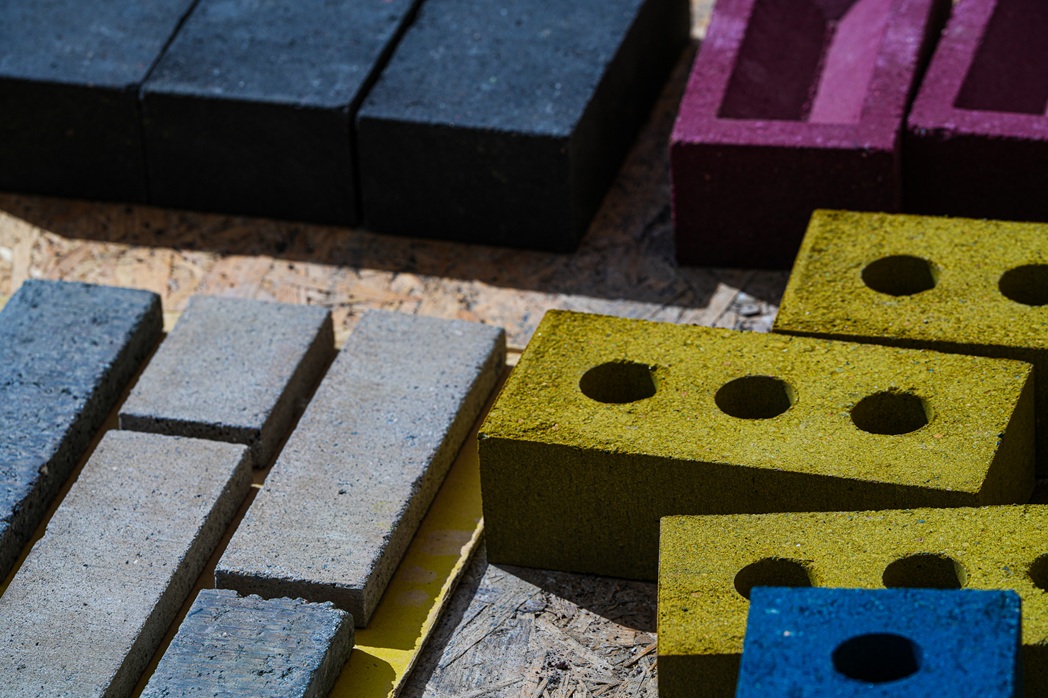
A brick produced from recycled construction and demolition waste has achieved certification from the construction certification body, the British Board of Agrément (BBA).
As one of the world’s most sustainable low-carbon bricks, the K-BRIQ from Scottish cleantech building materials company Kenoteq can now be confidently specified into a wide range of construction projects ranging from facades and feature walls to brick plinths.
Kenoteq is beginning commercial production of up to two million bricks annually. This will scale to four million as required, from its first production facility in East Lothian. The company then plans to set up regional production both in the UK and internationally to provide low carbon building products from local waste.
The unfired K-BRIQ, made from nearly 100% recycled construction and demolition waste, has been certified with the same accreditation as standard clay bricks, yet produces 95% less embodied carbon due to its innovative production process.
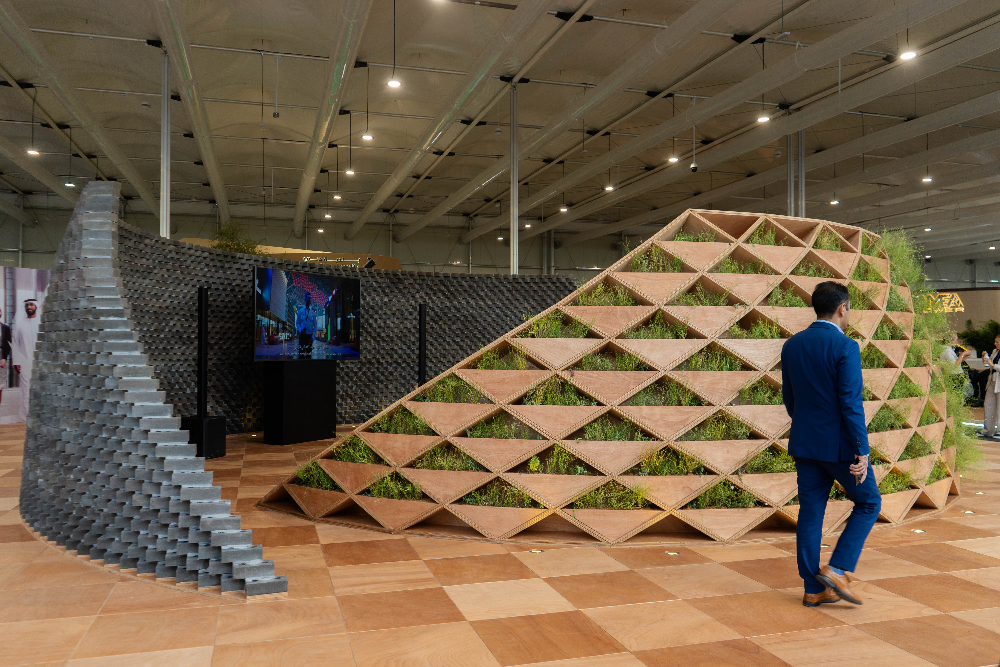
K-BRIQ showcase at COP28
With no standard testing regime for a non-traditional building material of this type, the K-BRIQ underwent an unprecedented level of rigorous testing over several years. Notably, it received the maximum durability rating possible, which is particularly important for the UK market.
Public sector organisations and developers in the City of London are already showing strong interest in the K-BRIQ’s environmental credentials as it can help meet their ambitious climate targets. Educational estates, large-scale office buildings and major urban regeneration projects are likely to be among early adopters.
This milestone follows additional certification for use in the United States through the prestigious DrJ Technical Evaluation Report (TER), positioning the K-BRIQ as a Scottish innovation preparing to make a global impact. With dual international certification secured, and European certification underway, the company is already fielding enquiries from across the world.
The K-BRIQ addresses significant environmental challenges in the construction industry. Today’s staple construction products drain finite resources while the sector is the largest contributor to landfill waste. The UK also relies on an environmentally damaging level of traditional high carbon brick imports. As Europe’s largest market for bricks, the UK uses around 2.5 billion bricks annually. With over 500 million imported and around 50 million of these travelling from outside the EU, the environmental impact is colossal.
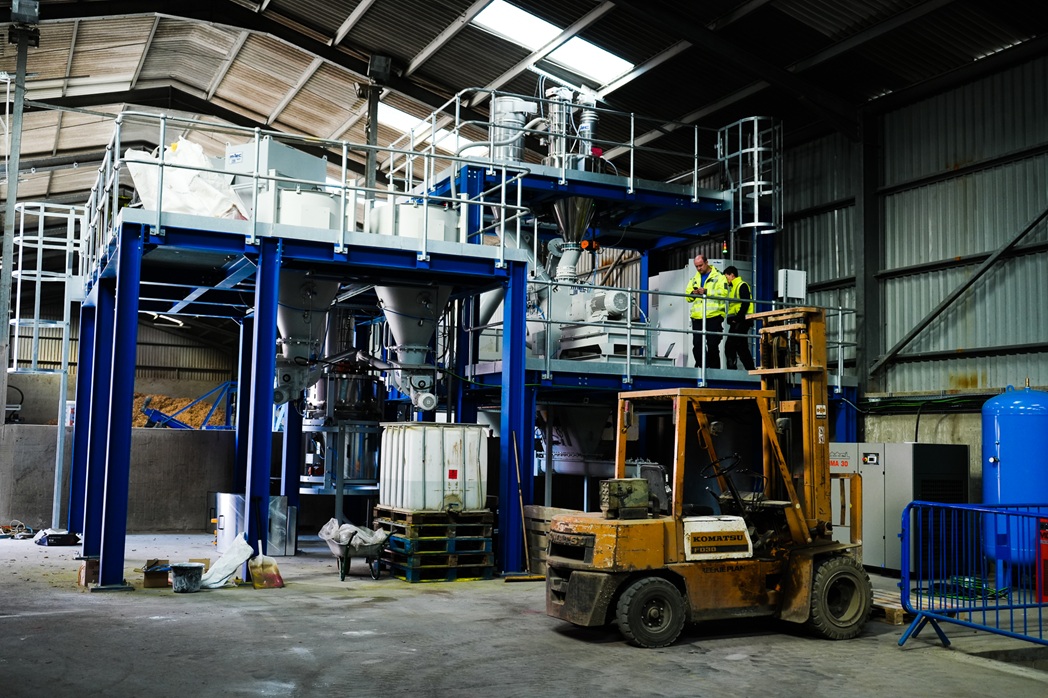
Additionally, more than a third of the waste in global landfills is estimated to be of demolition and construction origin. Construction, demolition and excavation waste accounts for approximately 60-65% of total waste generated in the UK, of which approximately 50-60 million tonnes is construction and demolition waste specifically. Tackling this, Kenoteq can create recycled bricks fit for use within 24 hours of the processed waste arriving at its ultra-low energy factory.
Sam Chapman, co-founder and executive director of Kenoteq, said: “This certification marks the arrival of a truly transformative building material for the construction and interior design industries. Unlike approaches that simply treat the symptoms of construction’s environmental impact, the K-BRIQ addresses the root cause by directly tackling the waste crisis while delivering a product that performs exactly like traditional materials, including the clay brick.
“Securing BBA certification allows our product to be specified with confidence on commercial projects across the UK. We’ve already seen significant interest from leading property developers, architectural firms and public sector bodies committed to reducing the carbon footprint of their construction projects.
“The K-BRIQ is not just an environmentally superior alternative to traditional bricks, but a technically robust building material suitable for a wide range of construction applications. With our certification secured, we can now scale up production to meet market requirements while maintaining the exceptional quality and sustainability credentials that set us apart.
“The construction industry is under increasing pressure to reduce its environmental impact while maintaining high standards of quality and safety. The BBA certification of the K-BRIQ demonstrates that these goals are not mutually exclusive – we can build better while building greener.”
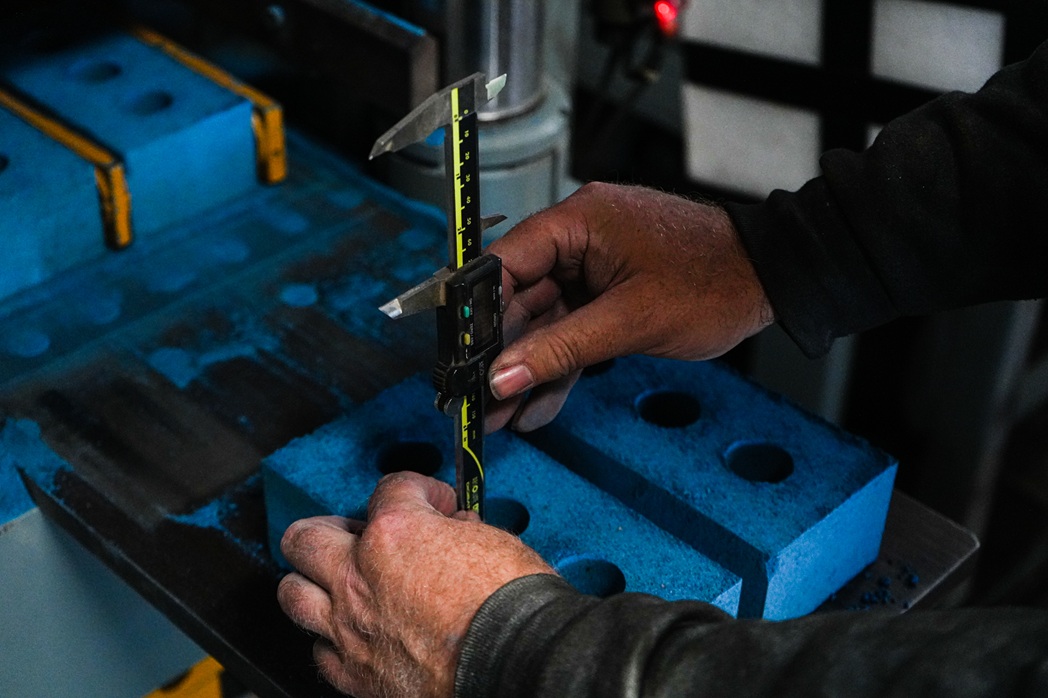
The K-BRIQ has achieved 100 tonnes of carbon savings in demonstration projects delivered to date. With 95% less embodied carbon than a traditional brick, the K-BRIQ represents a major advancement in sustainable construction materials at a time when embodied carbon is increasingly recognised as crucial to the whole-life carbon impact of buildings. Embodied carbon can account for over 50% of a building’s total carbon footprint, yet has received less attention than operational carbon in regulations and industry practices.
With a standard two-bedroom house in the UK typically requiring around 12,000 bricks, using a standard clay brick creates 5.46 tonnes of CO2e, a more comprehensive measurement than CO2 alone. Building with the K-BRIQ, in contrast, creates 0.2 tonnes of CO2e.
Katy Roberts, sales and marketing director at the British Board of Agrément, said: “The BBA is proud to play its part in helping clients like Kenoteq bring innovative and sustainable new products into the market. In a sector where safety, performance, and trust are non-negotiable, third-party certification plays a crucial role in enabling innovation.
“Independent certification provides a rigorous, evidence-based pathway for new products to gain market acceptance. It reassures stakeholders, supports regulatory compliance, and ultimately helps turn groundbreaking ideas into real-world construction solutions.”