Construction Leader: David Crawford on growing sustainably at Deeside Timberframe
David Crawford
In the first Construction Leaders feature of 2024, David Crawford talks to Margaret Taylor about his introduction to timber, the long-term sustainability benefits of the material and Deeside Timberframe’s expansion into England.
David Crawford is a timber evangelist. Having joined manufacturing business Deeside Timberframe in 2022, the managing director waxes lyrical about the benefits construction from timber can bring. It is more environmentally friendly than building with bricks or blocks because the amount of carbon emitted in the manufacturing process is significantly lower.
The raw material – trees – are also good for the environment because they sequester carbon from the atmosphere. And, although there is an impact, in that the majority of trees used in the industry, are imported from Scandinavia, the beauty of the product is, Crawford says, that it is sustainable.
“Net zero targets have been set by the UK Government and the construction industry is a significant contributing factor, the use of more timber is just one step, but in my view, it is key to long-term sustainability,” he said.
“During tree growth carbon dioxide is locked into the timber, but even when the raw material is processed, the same amount of carbon dioxide continues to be stored, throughout the life of the product. It’s particularly gratifying to note that for each tree harvested, three new trees are planted in its place. Not only ensuring sustainability but also contributing positively to the environment and future timber resources.”
David first became interested in timber while studying civil engineering at Edinburgh Napier University.
“I graduated slap-bang in the middle of the 2007-08 recession and there weren’t many jobs for graduate engineers but there had been different modules throughout the course and timber was always something that interested me,” he says. “Whilst studying I’d had some part-time jobs with construction companies and when timber was involved I always enjoyed it more.
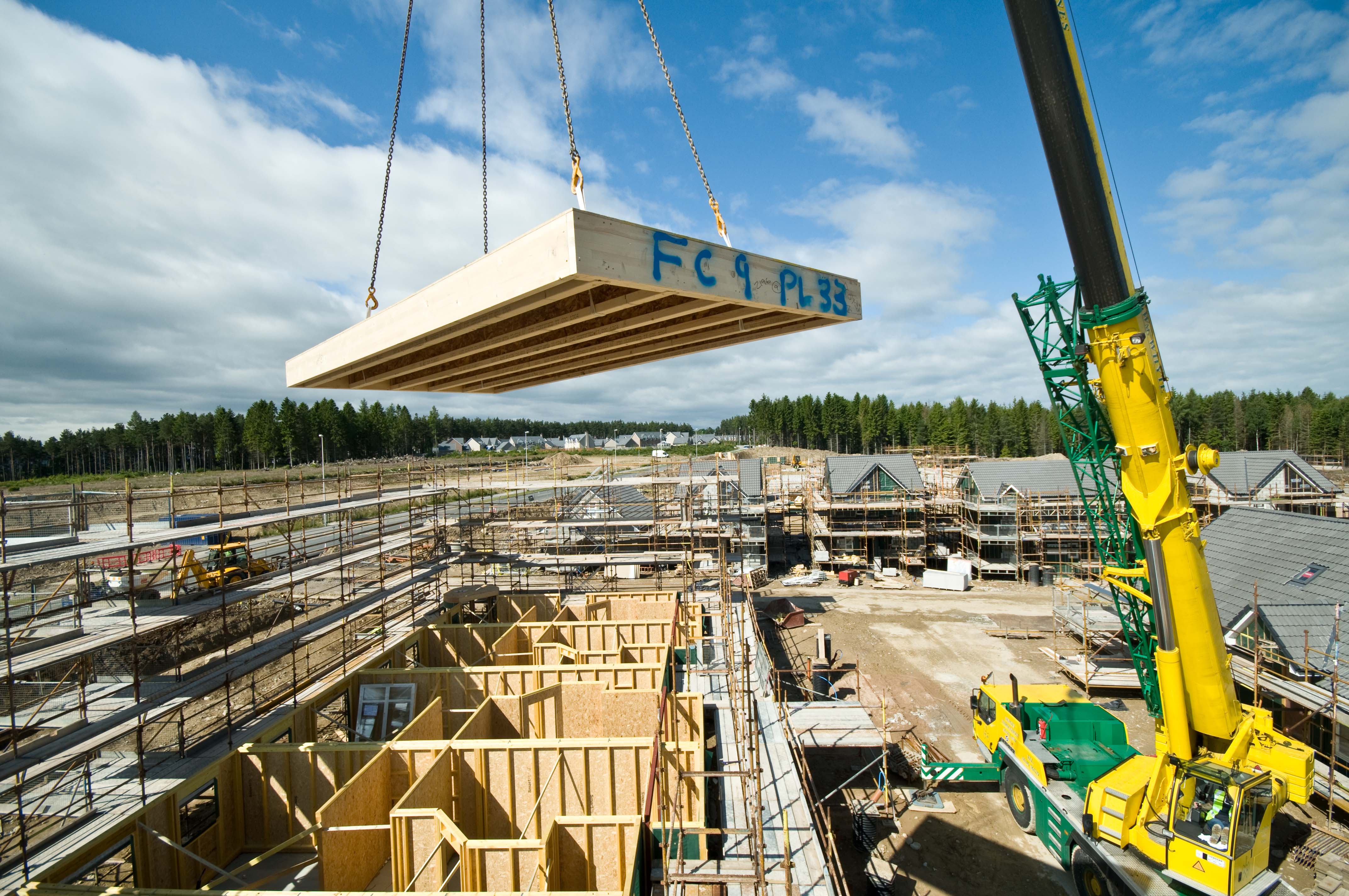
“When the recession hit the timing actually worked out well. Napier University had recently established a new Centre for Offsite Construction and the lecturer who was overseeing my thesis was heading that up. He was really supportive during my final year and encouraged me to stay on and do a Masters in timber engineering and work part-time at the centre. I completed my Master’s and started full-time with the University which was a really great opportunity.”
During his time working for Napier’s Centre for Offsite Construction & Innovative Structures, Crawford travelled to countries including Germany and Austria, where timber-frame construction is far more commonplace than in the UK, to learn about different approaches to housebuilding. That led to a full-time position with CCG, which he had been consulting for, and that ultimately led to him joining Deeside, which is part of the Banchory-based Bancon Group, in late 2022.
It has been an interesting time to take the helm, Crawford says, with the business, which has factories in Stonehaven and Stirling, securing its best-ever turnover – £39 million – two years ago. In the year to March 2023, the business turned over £37m and whilst market conditions will see a step back this financial year Crawford remains positive about the future outlook.
“The current economic conditions have resulted in a significant slowdown in construction and housebuilding activity,” he says. “Coming out of lockdown the majority of people were starting to appreciate their houses more and had money to spend on them and there had been a gap in new houses being constructed for first-time buyers entering the market. This, amongst other things, contributed to a significant surge in the market. Since then there has been high inflation, the rising cost of living, mortgage rate increases and the cost of materials and so the cost of constructing new-build homes got to a level that was probably unsustainable thus driving a downturn.”
Though any kind of slowdown can be a cause for concern, it can also present an opportunity. Crawford says that Deeside was so busy coming out of the pandemic that the pause in activity has given it the breathing space it needed to put in place his plan to prepare it for the next phase of growth.
“A lot of the changes we’ve already made would have been extremely difficult to implement if we were operating at full capacity,” he says. “We’ve been testing new software and bringing in new equipment to augment and expand our services. When you’re working to client deadlines it’s difficult to manage change, monitor success and identify areas that require refinement. In the next 18 to 24 months there’s a real opportunity for growth in the timber sector.”
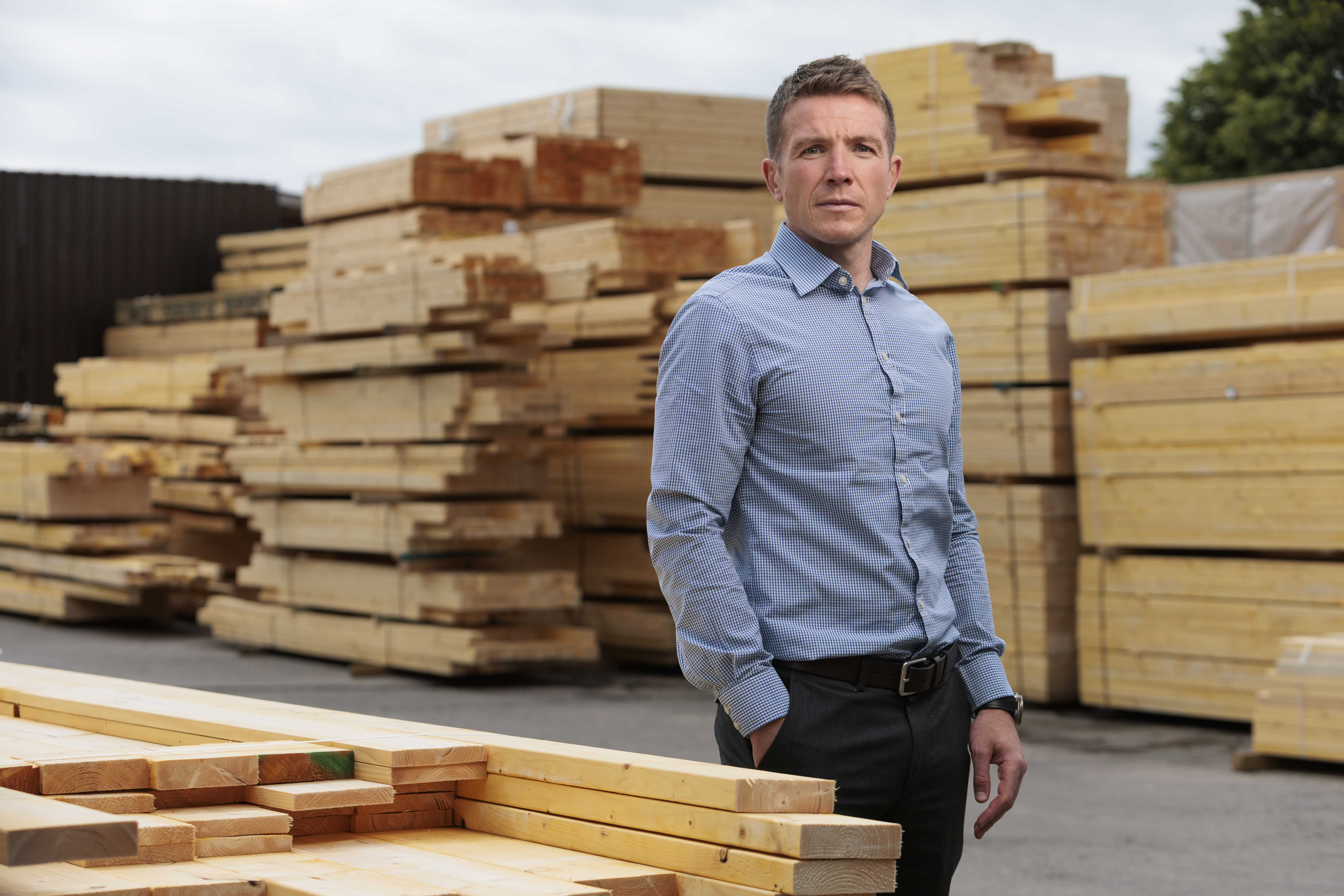
Much of that opportunity is likely to come south of the border. Deeside deliberately focused almost all its activities in Scotland in response to Covid but, with the Scottish timber-frame market already mature while the English market is in its infancy, Crawford says the company has recently begun looking at ways to take advantage of that.
“Over 90% of all new build homes in Scotland are delivered using timber frames, but in England, the proportion of timber-frame use is far less, approximately 10-15 per cent. Where the opportunity lies is due to the fact that Scotland typically build circa 22,500 homes per year and England approx. 172,500. Therefore, a nominal 10 per cent increase in England will generate nearly the same overall demand as the whole of Scotland.
“Deeside has been trading for over 35 years and has the knowledge, skillsets and capability to meet the growing demand in other geographic areas. Last year we started a sales manager in North West England and we are currently recruiting other key roles which will be the first key steps in driving forward our sustained presence.”
Many businesses across the construction sector are finding their growth plans are being hampered by an inability to find enough skilled labour, something Crawford says the entire industry has to take responsibility for. However, he notes that timber manufacturing is insulated from that to a degree because so much of the build process is done in a factory setting. That, he says, has a number of benefits.
“There’s a real shortage of labour across a lot of trades,” he says. “That was very apparent in the two years after Covid and we’re really starting to see the effects of that. There are not the same number of people doing apprenticeships and a lot of the existing workforce are more mature in years or have moved on to other jobs. As an industry we need to do more to support and encourage new generations into the industry.”
“Where timber frame and offsite technology can look to bridge the gap is by doing more in a factory environment. You can break down the processes that are done onsite and do more in a factory. By introducing automated computer-controlled technology to the design and manufacturing processes you create and safeguard jobs but also provide a platform for adaptability and repeatability.”
Crawford’s leadership at Deeside Timberframe emphasises a commitment to sustainable timber frame construction, looking beyond Scotland towards the English market. His proactive strategies reflect an understanding of the market’s potential, especially for sustainable solutions. As housing demand in the UK rises, Deeside’s investment in timber frame, a proven ‘Modern Method of Construction’, aligns with the UK’s goal to reduce carbon emissions whilst providing housing to all.